Table of contents
Barrel roller bearings
- Bearing design
- Load carrying capacity
- Compensation of angular misalignments
- Lubrication
- Sealing
- Speeds
- Noise
- Temperature range
- Cages
- Internal clearance
- Dimensions, tolerances
- Suffixes
- Structure of bearing designation
- Dimensioning
- Minimum load
- Design of bearing arrangements
- Mounting and dismounting
- Legal notice regarding data freshness
- Further information
Barrel roller bearings
Barrel roller bearings are suitable:
- for compensating angular misalignments where there is skewing between the outer and inner ring ➤ section
- where high radial shock type loads occur, as a result of the line contact ➤ section
- where angular misalignments and high radial loads occur, but speed is not a priority ➤ Figure
Barrel roller bearing: speed comparison with self-aligning ball bearing, compensation of misalignments Fr = radial load Cr = radial basic dynamic load rating |
![]() |
Bearing design
Design variants
Barrel roller bearings are available as:
Bearings of basic design
The outer ring has a curved raceway
Barrel roller bearings are single row, self-retaining radial roller bearings, which are part of the group of self-aligning bearings. The outer ring has a concave raceway. As a result, the bearings permit the compensation of static and dynamic angular misalignments (skewing between the inner and outer ring) within certain limits ➤ section. The inner ring has a formed raceway for the rolling elements and two rigid ribs. The rollers are barrel-shaped and are guided between the inner ring ribs. Their outside surface line closely follows the raceway profile of the outer and inner ring. Solid cages made from polyamide PA66 or brass are used ➤ Table.
The bore is cylindrical or tapered
Barrel roller bearings of basic design are available with a cylindrical or tapered bore, as a function of the bore diameter d ➤ Figure.
Bearings with a tapered bore have a bore taper of 1:12 and the suffix K ➤ Table.
Barrel roller bearings of basic design Fr = radial load Fa = axial load
|
![]() |
Bearings with adapter sleeve
Ready-to-fit bearing mounting kits facilitate the ordering and mounting of barrel roller bearings
Complete bearing mounting kits comprising the bearing of basic design, slotted adapter sleeve, tab washer and locknut, are also available for use in the location of barrel roller bearings with a tapered bore on a cylindrical shaft journal (series 202..-K + H, 203..-K + H) ➤ Figure. Adapter sleeves allow bearings to be located on smooth and stepped shafts. The adapter sleeves must also be stated when placing the order. Ordering example ➤ Figure.
Barrel roller bearing with adapter sleeve Fr = radial load Fa = axial load
|
![]() |
Load carrying capacity
Suitable for high radial loads
The balls are in line contact with the raceways. As a result, barrel roller bearings have a very high radial load carrying capacity ➤ Figure. In contrast, they have only a low axial load carrying capacity.
Axial load carrying capacity of bearings with adapter sleeve
Where bearings with adapter sleeves are located on a smooth shaft without a fixed stop (e. g. rigid shoulder), their axial load carrying capacity is dependent on the friction between the shaft and the sleeve.
If there is any uncertainty regarding the axial load carrying capacity of the adapter sleeve location method, please consult Schaeffler.
Compensation of angular misalignments
Barrel roller bearings compensate dynamic and static angular misalignments
Due to the concave rolling element raceway in the outer ring, barrel roller bearings are capable of angular adjustment ➤ section. As a result, they permit skewing between the outer and inner ring within certain limits, without causing damage to the bearings, and can thus compensate misalignments, shaft deflections and housing deformations.
Permissible adjustment angle
With a rotating inner ring, barrel roller bearings can swivel up to 4° from their central position
The magnitude of alignment and angular defects may only be so large when the bearings are mounted that the contact surfaces of the rolling elements under load still lie within the width of the raceway. Under normal operating conditions and with a rotating inner ring, barrel roller bearings can swivel by up to 4° from their central position. The extent to which this value can be used for skewing between the inner and outer ring is, however, essentially dependent on the design of the bearing arrangement.
If the outer ring rotates or the inner ring undergoes tumbling motion, the angular adjustment facility is smaller. In such cases, please consult Schaeffler.
Lubrication
Oil or grease lubrication
The bearings are not greased. They must be lubricated with oil or grease and can be lubricated from the end faces.
Compatibility with plastic cages
When using bearings with plastic cages, compatibility between the lubricant and the cage material must be ensured if synthetic oils, lubricating greases with a synthetic oil base or lubricants containing a high proportion of EP additives are used.
Observe oil change intervals
Aged oil and additives in the oil can impair the operating life of plastics at high temperatures. As a result, stipulated oil change intervals must be strictly observed.
Sealing
The bearings are open; providing additional seals in the adjacent construction
Barrel roller bearings are supplied without seals. As a result, sealing of the bearing position must be carried out in the adjacent construction. The sealing system should reliably prevent:
- moisture and contaminants from entering the bearing
- the egress of lubricant from the bearing position
Speeds
The product tables give the limiting speed nG. This is the kinematically permissible speed of a bearing. Even under favourable mounting and operating conditions, this value should not be exceeded without prior consultation with Schaeffler ➤ link.
Noise
Schaeffler Noise Index
The Schaeffler Noise Index (SGI) is not yet available for this bearing type ➤ link. The data for these bearing series will be introduced and updated in stages.
Temperature range
Limiting values
The operating temperature of the bearings is limited by:
- the dimensional stability of the bearing rings and rolling elements
- the cage
- the lubricant
Possible operating temperatures of barrel roller bearings ➤ Table.
Permissible temperature ranges
Operating temperature |
Barrel roller bearings |
|
---|---|---|
with brass cage |
with polyamide cage PA66 |
|
|
–30 °C to +150 °C, |
–30 °C to +120 °C |
In the event of anticipated temperatures which lie outside the stated values, please contact Schaeffler.
Cages
Standard cages for barrel roller bearings ➤ Table.
Cage, cage suffix, bore code
Bearing series |
Solid cage |
Solid brass cage |
---|---|---|
TVP |
MB |
|
Bore code |
||
202 |
up to 16 |
from 17 |
203 |
up to 12 |
from 13 |
For high continuous temperatures and applications with difficult operating conditions, bearings with brass cages should be used. If there is any uncertainty regarding cage suitability, please consult Schaeffler.
Internal clearance
Radial internal clearance – bearings with cylindrical bore
The standard is CN
Barrel roller bearings with cylindrical bore are manufactured as standard with radial internal clearance CN (normal) ➤ Table. CN is not stated in the designation.
Certain sizes are also available by agreement with the smaller internal clearance C2 and with the larger internal clearance C3 and C4.
Values for radial internal clearance ➤ Table. These are valid for bearings which are free from load and measurement forces (without elastic deformation).
Radial internal clearance of barrel roller bearings with cylindrical bore
Nominal |
Radial internal clearance |
||||||||
---|---|---|---|---|---|---|---|---|---|
d |
C2 |
CN |
C3 |
C4 |
|||||
mm |
μm |
μm |
μm |
μm |
|||||
over |
incl. |
min. |
max. |
min. |
max. |
min. |
max. |
min. |
max. |
– |
30 |
2 |
9 |
9 |
17 |
17 |
28 |
28 |
40 |
30 |
40 |
3 |
10 |
10 |
20 |
20 |
30 |
30 |
45 |
40 |
50 |
3 |
13 |
13 |
23 |
23 |
35 |
35 |
50 |
50 |
65 |
4 |
15 |
15 |
27 |
27 |
40 |
40 |
55 |
65 |
80 |
5 |
20 |
20 |
35 |
35 |
55 |
55 |
75 |
80 |
100 |
7 |
25 |
25 |
45 |
45 |
65 |
65 |
90 |
continued ▼ |
Radial internal clearance of barrel roller bearings with cylindrical bore
Nominal |
Radial internal clearance |
||||||||
---|---|---|---|---|---|---|---|---|---|
d |
C2 |
CN |
C3 |
C4 |
|||||
mm |
μm |
μm |
μm |
μm |
|||||
over |
incl. |
min. |
max. |
min. |
max. |
min. |
max. |
min. |
max. |
100 |
120 |
10 |
30 |
30 |
50 |
50 |
70 |
70 |
95 |
120 |
140 |
15 |
35 |
35 |
55 |
55 |
80 |
80 |
110 |
140 |
160 |
20 |
40 |
40 |
65 |
65 |
95 |
95 |
125 |
160 |
180 |
25 |
45 |
45 |
70 |
70 |
100 |
100 |
130 |
180 |
225 |
30 |
50 |
50 |
75 |
75 |
105 |
105 |
135 |
225 |
250 |
35 |
55 |
55 |
80 |
80 |
110 |
110 |
140 |
250 |
280 |
40 |
60 |
60 |
85 |
85 |
115 |
115 |
145 |
continued ▲ |
Radial internal clearance – bearings with tapered bore
C3 is normally used
Barrel roller bearings with tapered bore are normally manufactured with the larger radial internal clearance C3 ➤ Table.
Certain sizes are also available by agreement with the smaller internal clearance C2, with internal clearance CN (normal) and with the larger internal clearance C4.
Values for radial internal clearance ➤ Table. These are valid for bearings which are free from load and measurement forces (without elastic deformation).
Radial internal clearance of barrel roller bearings with tapered bore
Nominal |
Radial internal clearance |
||||||||
---|---|---|---|---|---|---|---|---|---|
d |
C2 |
CN |
C3 |
C4 |
|||||
mm |
μm |
μm |
μm |
μm |
|||||
over |
incl. |
min. |
max. |
min. |
max. |
min. |
max. |
min. |
max. |
– |
30 |
9 |
17 |
17 |
28 |
28 |
40 |
40 |
55 |
30 |
40 |
10 |
20 |
20 |
30 |
30 |
45 |
45 |
60 |
40 |
50 |
13 |
23 |
23 |
35 |
35 |
50 |
50 |
65 |
50 |
65 |
15 |
27 |
27 |
40 |
40 |
55 |
55 |
75 |
65 |
80 |
20 |
35 |
35 |
55 |
55 |
75 |
75 |
95 |
80 |
100 |
25 |
45 |
45 |
65 |
65 |
90 |
90 |
120 |
100 |
120 |
30 |
50 |
50 |
70 |
70 |
95 |
95 |
125 |
120 |
140 |
35 |
55 |
55 |
80 |
80 |
110 |
110 |
140 |
140 |
160 |
40 |
65 |
65 |
95 |
95 |
125 |
125 |
155 |
160 |
180 |
45 |
70 |
70 |
100 |
100 |
130 |
130 |
160 |
180 |
225 |
50 |
75 |
75 |
105 |
105 |
135 |
135 |
165 |
225 |
250 |
55 |
80 |
80 |
110 |
110 |
140 |
140 |
170 |
250 |
280 |
60 |
85 |
85 |
115 |
115 |
145 |
145 |
175 |
Dimensions, tolerances
Dimension standards
The main dimensions of barrel roller bearings correspond to DIN 635‑1:2010. Nominal dimensions of barrel roller bearings ➤ link.
Chamfer dimensions
The limiting dimensions for chamfer dimensions correspond to DIN 620‑6:2004. Overview and limiting values ➤ section. Nominal value of chamfer dimension ➤ link.
Tolerances
The tolerances for the dimensional and running accuracy of barrel roller bearings correspond to tolerance class Normal in accordance with ISO 492:2014. Tolerance values in accordance with ISO 492 ➤ link.
Suffixes
For a description of the suffixes used in this chapter see ➤ Table and medias interchange http://www.schaeffler.de/std/1B69.
Suffixes and corresponding descriptions
Suffix |
Description of suffix |
|
---|---|---|
C2 |
Radial internal clearance C2 (smaller than normal) |
Special design, available by agreement |
C3 |
Radial internal clearance C3 (larger than normal) |
Normally used for bearings with tapered bore, available by agreement |
C4 |
Radial internal clearance C4 (larger than C3) |
Special design, available by agreement |
CN |
Radial internal clearance CN (normal) |
Normally used for bearings with cylindrical bore, available by agreement for bearings with tapered bore |
K |
Tapered bore, taper 1:12 |
Standard |
MB |
Solid brass cage, guided on inner ring |
Standard, cage material dependent on bore code |
TVP |
Solid cage made from glass fibre reinforced polyamide PA66 |
Standard, cage material dependent on bore code |
Structure of bearing designation
Examples of composition of bearing designation
The designation of bearings follows a set model. Examples ➤ Figure and ➤ Figure. The composition of designations is subject to DIN 623‑1➤ Figure.
Barrel roller bearing with cylindrical bore: designation structure |
![]() |
Barrel roller bearing with tapered bore and adapter sleeve: designation structure |
![]() |
Dimensioning
Equivalent dynamic bearing load
P = Fr under purely radial load of constant magnitude and direction
The basic rating life equation L = (Cr/P)p used in the dimensioning of bearings under dynamic load assumes a load of constant magnitude and direction. In radial bearings, this is a purely radial load Fr. If this condition is met, the bearing load Fr is used in the rating life equation for P (P = Fr).
P is a substitute force for combined load and various load cases
If this condition is not met, a constant radial force must first be determined for the rating life calculation that (in relation to the rating life) represents an equivalent load. This force is known as the equivalent dynamic bearing load P.
To calculate P for barrel roller bearings under dynamic load ➤ Equation.
Equivalent dynamic load

Legend
P | N |
Equivalent dynamic bearing load |
Fr | N |
Radial load |
Fa | N |
Axial load |
Equivalent static bearing load
For barrel roller bearings subjected to static load ➤ Equation.
Equivalent static load

Legend
P0 | N |
Equivalent static bearing load |
F0r, F0a | N |
Largest radial or axial load present (maximum load) |
Static load safety factor
S0 = C0/P0
In addition to the basic rating life L (L10h), it is also always necessary to check the static load safety factor S0 ➤ Equation.
Static load safety factor
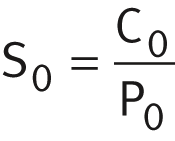
Legend
S0 | - |
Static load safety factor |
C0 | N |
Basic static load rating |
P0 | N |
Equivalent static bearing load |
Minimum load
In order to prevent damage due to slippage, a minimum radial load of P > C0r/60 is required
In order that no slippage occurs between the contact partners, the barrel roller bearings must be constantly subjected to a sufficiently high load. Based on experience, a minimum radial load of the order of P > C0r/60 is thus necessary. In most cases, however, the radial load is already higher than the requisite minimum load due to the weight of the supported parts and the external forces.
If the minimum radial load is lower than indicated above, please consult Schaeffler.
Design of bearing arrangements
Support bearing rings over their entire circumference and width
In order to allow full utilisation of the load carrying capacity of the bearings and thus also achieve the requisite rating life, the bearing rings must be rigidly and uniformly supported by means of contact surfaces over their entire circumference and over the entire width of the raceway. Support can be provided by means of a cylindrical or tapered seating surface ➤ Figure to ➤ Figure. The seating and contact surfaces should not be interrupted by grooves, holes or other recesses. The accuracy of mating parts must meet specific requirements ➤ Table to ➤ Table.
Radial location – fit recommendations for bearings with cylindrical bore
For secure radial location, tight fits are necessary
In addition to supporting the rings adequately, the bearings must also be securely located in a radial direction, to prevent creep of the bearing rings on the mating parts under load. This is generally achieved by means of tight fits between the bearing rings and the mating parts. If the rings are not secured adequately or correctly, this can cause severe damage to the bearings and adjacent machine parts. Influencing factors, such as the conditions of rotation, magnitude of the load, internal clearance, temperature conditions, design of the mating parts and the mounting and dismounting options must be taken into consideration in the selection of fits.
If shock type loads occur, tight fits (transition fit or interference fit) are required to prevent the rings from coming loose at any point. Clearance, transition or interference fits ➤ Table and ➤ Table.
The following information provided in Technical principles must be taken into consideration in the design of bearing arrangements:
- conditions of rotation ➤ link
- tolerance classes for cylindrical shaft seats (radial bearings) ➤ link
- shaft fits ➤ link
- tolerance classes for bearing seats in housings (radial bearings) ➤ link
- housing fits ➤ link
- shaft tolerances for adapter sleeves and withdrawal sleeves ➤ link
Axial location – fit recommendations for bearings with cylindrical bore
The bearings must also be securely located in an axial direction
As a tight fit alone is not normally sufficient to also locate the bearing rings securely on the shaft and in the housing bore in an axial direction, this must usually be achieved by means of an additional axial location or retention method. The axial location of the bearing rings must be matched to the type of bearing arrangement. Shaft and housing shoulders, housing covers, nuts, spacer rings, retaining rings, adapter and withdrawal sleeves etc. are generally suitable.
Location of bearings with tapered bore
Location by means of locknut and tab washer
If a bearing with a tapered bore is mounted directly on a tapered journal the bearing can be axially located with ease using an axial locknut and tab washer ➤ Figure.
Barrel roller bearing with tapered bore, mounted directly on the tapered shaft jounal
|
![]() |
Location of bearings by means of adapter sleeve
Mounting can be carried out quickly and reliably by means of wrench sets from Schaeffler
Barrel roller bearings with a tapered bore can be located easily and reliably on smooth or stepped shafts by means of an adapter sleeve ➤ Figure. The adapter sleeves do not need to be secured on the shaft by any additional means. The bearings can be positioned at any point on smooth shafts. Axial load carrying capacity of bearing arrangements by means of adapter sleeve connection ➤ section.
Barrel roller bearing with adapter sleeve, located on smooth shaft
|
![]() |
Location by means of adapter sleeve, axial support by means of a support ring
If very high axial forces are present, a support ring can also be used to provide axial support ➤ Figure. In this instance, the mounting dimensions of the support ring Ba and db in the product tables must be observed ➤ link.
Stepped shaft, axial support by means of a support ring
|
![]() |
Dimensional, geometrical and running accuracy of cylindrical bearing seats
A minimum of IT6 should be provided for the shaft seat and a minimum of IT7 for the housing seat
The accuracy of the cylindrical bearing seat on the shaft and in the housing should correspond to the accuracy of the bearing used. For barrel roller bearings with the tolerance class Normal, the shaft seat should correspond to a minimum of standard tolerance grade IT6 and the housing seat to a minimum of IT7. Guide values for the geometrical and positional tolerances of bearing seating surfaces ➤ Table, tolerances t1 to t3 in accordance with ➤ Figure. Numerical values for IT grades ➤ Table.
Guide values for the geometrical and positional tolerances of bearing seating surfaces
Bearing |
Bearing seating surface |
Standard tolerance grades to ISO 286-1 |
||||
---|---|---|---|---|---|---|
to ISO 492 |
to DIN 620 |
Diameter tolerance |
Roundness tolerance |
Parallelism tolerance |
Total axial runout tolerance of abutment shoulders |
|
t1 |
t2 |
t3 |
||||
Normal |
PN (P0) |
Shaft |
IT6 (IT5) |
Circumferential load IT4/2 |
Circumferential load IT4/2 |
IT4 |
Shaft | IT6 (IT5) |
Point load IT5/2 |
Point load IT5/2 |
IT4 | ||
Housing |
IT7 (IT6) |
Circumferential load IT5/2 |
Circumferential load IT5/2 |
IT5 |
||
Housing | IT7 (IT6) |
Point load IT6/2 |
Point load IT6/2 |
IT5 |
Numerical values for ISO standard tolerances (IT grades) to ISO 286-1:2010
IT grade |
Nominal dimension in mm |
|||||||
---|---|---|---|---|---|---|---|---|
over |
18 |
30 |
50 |
80 |
120 |
180 |
250 |
|
incl. |
30 |
50 |
80 |
120 |
180 |
250 |
315 |
|
Values in μm |
||||||||
IT4 |
6 | 7 | 8 | 10 | 12 | 14 | 16 | |
IT5 |
9 | 11 | 13 | 15 | 18 | 20 | 23 | |
IT6 |
13 | 16 | 19 | 22 | 25 | 29 | 32 | |
IT7 |
21 | 25 | 30 | 35 | 40 | 46 | 52 |
Roughness of cylindrical bearing seating surfaces
Ra must not be too high
The roughness of the bearing seats must be matched to the tolerance class of the bearings. The mean roughness value Ra must not be too high, in order to maintain the interference loss within limits. The shafts must be ground, while the bores must be precision turned. Guide values as a function of the IT grade of bearing seating surfaces ➤ Table.
Roughness values for cylindrical bearing seating surfaces – guide values
Nominal diameter d (D) |
Recommended mean roughness value Ramax |
||||
---|---|---|---|---|---|
mm |
μm |
||||
Diameter tolerance (IT grade) |
|||||
over |
incl. |
IT7 |
IT6 |
IT5 |
IT4 |
‒ |
80 |
1,6 |
0,8 |
0,4 |
0,2 |
80 |
500 |
1,6 |
1,6 |
0,8 |
0,4 |
Tolerances for tapered bearing seats
Specifications for tapered bearing seats
For bearings located directly on a tapered shaft journal, ➤ Figure, the data are in accordance with ➤ Figure.
Mounting dimensions for the contact surfaces of bearing rings
The contact surfaces for the rings must be of sufficient height
The mounting dimensions of the shaft and housing shoulders, and spacer rings etc., must ensure that the contact surfaces for the bearing rings are of sufficient height. However, they must also reliably prevent rotating parts of the bearing from grazing stationary parts. Proven mounting dimensions for the radii and diameters of the abutment shoulders are indicated in the product tables. These dimensions are limiting dimensions (maximum or minimum dimensions); the actual values should not be higher or lower than specified.
Suitable bearing housings for barrel roller bearings
A large range of housings is available
For economical, operationally reliable and easily interchangeable bearing arrangement units, the barrel roller bearings can also be combined with Schaeffler bearing housings ➤ Figure. These easy-to-fit units fulfil all of the requirements for modern machine and plant designs with favourable maintenance-related characteristics.
Due to the large number of application areas, an extensive range of split plummer block housings and flanged housings is available for bearings with cylindrical and tapered bores. Detailed information on bearing housings can be found in publication GK 1 http://www.schaeffler.de/std/1B63. This book can be ordered from Schaeffler.
Split plummer block housing with a barrel roller bearing
|
![]() |
Mounting and dismounting
The mounting and dismounting options for barrel roller bearings, by thermal, hydraulic or mechanical methods, must be taken into consideration in the design of the bearing position.
Ensure that the bearings are not damaged during mounting
Barrel roller bearings are not separable. In the mounting of non-separable bearings, the mounting forces must always be applied to the bearing ring with a tight fit.
Bearings with tapered bore – methods for achieving a sufficiently tight fit
Suitable methods: measuring the reduction in radial internal clearance or axial displacement
Bearings with a tapered bore are mounted with a tight fit on the shaft or adapter and withdrawal sleeve. The tight fit can be checked:
- by measuring the reduction in radial internal clearance or
- by measuring the axial displacement of the inner ring on the tapered bearing seat
The malfunction-free operation of barrel roller bearings presupposes that these have been mounted correctly. An insufficient operating clearance or inadequately tight fit on the shaft generally leads to bearing damage.
If there is any uncertainty regarding the practical application of both methods, Schaeffler must always be consulted.
Schaeffler Mounting Handbook
Rolling bearings must be handled with great care
Rolling bearings are well-proven precision machine elements for the design of economical and reliable bearing arrangements, which offer high operational security. In order that these products can function correctly and achieve the envisaged operating life without detrimental effect, they must be handled with care.
The Schaeffler Mounting Handbook MH 1 gives comprehensive information about the correct storage, mounting, dismounting and maintenance of rotary rolling bearings http://www.schaeffler.de/std/1B68. It also provides information which should be observed by the designer, in relation to the mounting, dismounting and maintenance of bearings, in the original design of the bearing position. This book is available from Schaeffler on request.
Legal notice regarding data freshness
The further development of products may also result in technical changes to catalogue products
Of central interest to Schaeffler is the further development and optimisation of its products and the satisfaction of its customers. In order that you, as the customer, can keep yourself optimally informed about the progress that is being made here and with regard to the current technical status of the products, we publish any product changes which differ from the printed version in our electronic product catalogue.
We therefore reserve the right to make changes to the data and illustrations in this catalogue. This catalogue reflects the status at the time of printing. More recent publications released by us (as printed or digital media) will automatically precede this catalogue if they involve the same subject. Therefore, please always use our electronic product catalogue to check whether more up-to-date information or modification notices exist for your desired product.
Further information
In addition to the data in this chapter, the following chapters in Technical principles must also be observed in the design of bearing arrangements: